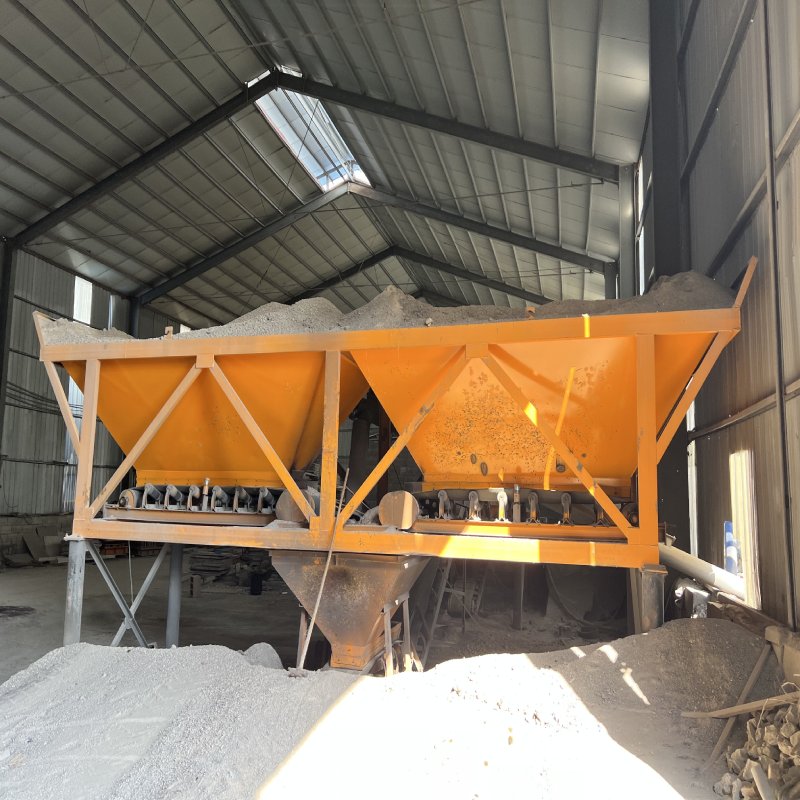
Image source:Aiwei block machine
Introduction
The concrete block manufacturing industry stands at the intersection of tradition and innovation, offering durable building materials while adapting to modern construction demands. As a cornerstone of the construction sector, this industry faces a myriad of challenges and opportunities that reflect the dynamic landscape of global development. In this article, we delve into the intricate web of challenges and opportunities that define concrete block manufacturing, exploring how industry players navigate these dynamics to remain competitive, sustainable, and adaptable in a rapidly evolving world.
1. The Landscape of Concrete Block Manufacturing
Concrete blocks are fundamental components of construction, providing structural integrity and design versatility. However, the industry is not immune to the external factors and internal dynamics that shape its trajectory.
- Market Demand: The demand for concrete blocks fluctuates with economic cycles and trends in construction activity.
- Sustainability Pressure: Increasing environmental awareness urges the industry to adopt eco-friendly practices and materials.
- Technological Advancements: Automation, digitalization, and smart technologies are reshaping production processes.
2. Challenges in Concrete Block Manufacturing
The concrete block manufacturing industry faces a range of challenges that require strategic solutions for sustained growth.
- Raw Material Sourcing: Dependence on raw materials like sand and aggregates exposes manufacturers to environmental concerns and resource scarcity.
- Energy Consumption: The energy-intensive nature of block production contributes to carbon emissions and operational costs.
- Waste Management: Handling waste generated during production and discarded blocks is a logistical and environmental challenge.
3. Sustainable Practices as Opportunities
Amid challenges, concrete block manufacturers are finding opportunities in sustainable practices that align with global environmental goals.
- Recycled Aggregates: Utilizing recycled materials reduces reliance on virgin resources and contributes to circular economy principles.
- Energy-Efficient Production: Advanced machines and processes optimize energy usage, lowering emissions and operational costs.
- Innovative Designs: Eco-friendly blocks with improved thermal properties enhance building efficiency and sustainability.
4. Innovations in Production Technology
Concrete block manufacturing is undergoing a transformation through the integration of technology, paving the way for increased efficiency and improved quality.
- Automation: Automated block making machines streamline production, reduce human error, and enhance consistency.
- Digitalization: Digital tools and software aid in design, scheduling, and inventory management, optimizing production processes.
- Quality Control: Technology allows for real-time monitoring of block quality, minimizing defects and waste.
5. Customization and Design Flexibility
Customization is emerging as a competitive edge, allowing manufacturers to cater to diverse architectural preferences and market demands.
- Architectural Aesthetics: Manufacturers can produce blocks with unique textures, patterns, and designs that align with architectural visions.
- Client-Centric Approach: Customization fosters client engagement, enabling manufacturers to tailor products to specific project requirements.
6. Market Trends and Niche Segments
Concrete block manufacturers are capitalizing on evolving market trends and catering to niche segments to diversify their offerings.
- Green Building: Eco-conscious consumers and sustainability mandates drive demand for energy-efficient and eco-friendly building materials.
- Urbanization and Modern Designs: Urban development and contemporary architectural trends create opportunities for innovative block designs.
7. Collaboration and Partnerships
The industry’s complex challenges often necessitate collaboration and partnerships to overcome obstacles collectively.
- Supply Chain Collaboration: Partnerships with raw material suppliers and logistics providers enhance efficiency and reduce costs.
- Architect-Industry Collaboration: Collaborative design efforts with architects foster innovation and cater to unique project requirements.
8. Training and Skill Development
As the industry embraces technology, a skilled workforce is essential for operating and maintaining modern production equipment.
- Technical Training: Operators require training to understand the complexities of automated machines and digital tools.
- Continuous Learning: Continuous skill development ensures that workers remain adept at using new technologies and techniques.
9. Regulatory Compliance and Standards
Adhering to construction and environmental regulations is critical for manufacturers to operate responsibly and ensure product quality.
- Quality Standards: Following industry standards ensures that blocks meet structural and safety requirements, enhancing market reputation.
- Environmental Regulations: Compliance with emissions and waste management regulations contributes to sustainability goals.
Conclusion: Paving the Path Forward
The concrete block manufacturing industry is a microcosm of the broader construction landscape, shaped by challenges and illuminated by opportunities. While resource scarcity, environmental concerns, and technological advancements present hurdles, they also open doors to innovation, collaboration, and sustainable practices. By embracing eco-friendly materials, leveraging technology, and nurturing a skilled workforce, concrete block manufacturers can navigate these dynamics to build a resilient and prosperous future. In a world that demands efficient, durable, and sustainable building materials, the industry’s ability to adapt and innovate will be pivotal in shaping the landscapes of tomorrow.